Automatic Blind System
Hi there,
I'm currently working on project call automatic blind system which is activate depends on outside condition. Before this is tried to build this project MICROCONTROLLER BASED AUTOMATED LIGHT CONTROL SYSTEM which is based on AVR ATMEGA32 but it failed to get what is has supposed to..
Since that i try to switch to PIC and found out using PBP is time saving and cost reduced language since the project submission is just around the corner..I hope PBP master here can fix my code since i wrote this just a day ago with zero knowledge of PBP by just reviewing the manual and project book. Here is the circuit diagram and code. The proteus VSM files will be PM if someone really want to help.
The Circuit
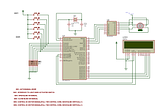
PicBasic Pro code
Code:
'****************************************************************
'* Name : 877A_BLIND.BAS *
'* Author : PIJO RAHMAN *
'* Notice : Copyright (c) 2008 [select VIEW...EDITOR OPTIONS] *
'* : All Rights Reserved *
'* Date : 11/4/2008 *
'* Version : 1.0 *
'* Notes : Using PIC16F877A to control Vertical Blind Auto *
'* and Manual with light sensor *
'****************************************************************
DEFINE OSC 4
'****************************************************************
CMCON = 7
ADCON1 = 7
TRISB = 0 ' Set PortB as output
TRISA = 1 ' Or TRISA = 255, set PortA as input
'***************************************************************
Define LCD_DREG PORTD 'Based on Rentron 877A LCD Connection
Define LCD_DBIT 4
Define LCD_RSREG PORTE
Define LCD_RSBIT 0
Define LCD_EREG PORTE
Define LCD_EBIT 1
B1 VAR BYTE 'Declared Byte For LCD Splash Screen
B0 VAR BYTE
B2 VAR BYTE
B3 VAR BYTE
B4 VAR BYTE
B5 VAR BYTE
'****************************************************************
clear 'clear all variables
LCDOUT $FE,1 'clear lcd
PAUSE 500 'pause for lcd init
Low PORTE.2 'LCD R/W line low (W)
'**************************************************************
'*****************slide text for splash screen**************************
LOOP:
LCDOut $fe,2
For B2= 0 TO 15
LookUp B0, [" AUTOMATIC BLIND SYSTEM #"], B1
IF B1 = "#" Then GoTo reset
LCDOut B1
B0 = B0 + 1
Next B2
pause 125 'character wait time
B0 = B0 - 15
GoTo loop
RESET:
LCDOUT $FE,1
'************************************************************************
CREDIT: 'Display Presenter Credit
LCDOUT $FE,$80
LCDOUT "PRESENTER NAME" 'presenter credit
'LCDOUT $FE,$C0
'LCDOUT " GROUP " 'presenter credit
PAUSE 1500
LCDOUT $FE,1
speed var word
speed = 100
;i var byte
Main: ' Main Prgm, Check Button for Auto/Manual Op
IF PORTA.0=1 THEN Manual
If PORTA.1=1 Then ForwardM
If PORTA.1=0 Then ReversesM
Goto Main
End
Manual: 'FOR MANUAL OPERATION START WITH RA0=1 THEN CONTROL RA2 AND RA3
Pause 500 'Do it about 2 times a second
LCDOUT $FE,1 'Clear LCD
LCDOUT $FE,$80,"MANUAL" 'Display "Manual" 1st Line on LCD
LCDOUT $FE,$C0,"USER INPUT" 'Display "USER INPUT" 2nd Line on LCD
IF PORTA.2=1 THEN FORWARDM 'Manually Opening Blind
IF PORTA.3=1 Then ReversesM 'Manually Closing Blind
Goto Main
ForwardM:
LCDOUT $FE,1
LCDOUT $FE,$80,"OPENING BLIND"
LCDOUT $FE,$C0,"DAYLIGHT"
;FOR i = 1 TO 5 ' one revolution 'Actually Use this Function for Revolution Step But No LUCK! :(
GOto Forward ' rotate clockwise
;NEXT i
GOTO Main
ReversesM:
LCDOUT $FE,1 'Clear LCD
LCDOUT $FE,$80,"CLOSING BLIND"
LCDOUT $FE,$C0,"SUNSET/DARK"
;FOR i = 1 TO 5 ' one revolution
Goto Reverses ' rotate counter-clockwise
;NEXT i
GOTO Main
Forward: 'Stepper Motor Clockwise Sequence
portb = %1100
pause speed
portb = %0110
pause speed
portb = %0011
pause speed
portb = %1001
pause speed
Goto Main
Reverses: 'Stepper Motor AntiClockwise Sequence
portb = %1001
pause speed
portb = %0011
pause speed
portb = %0110
pause speed
portb = %1100
pause speed
Goto Main
END
The operation
This project is simple as it shows. The circuit is consist of manual and automatic function. SW1 connected at RA0 is to use to switch between auto/manual mode. In auto mode, all the manual control switch which is SW3 and SW4 is not activated but only receive the signal from SW2 [which is will be interface to light-dark activated switch, so no ADC will be required]. If SW2 high, motor is rotate clockwise and the blind is open, but if SW2 low, motor is rotate anticlockwise and the blind is close.It need 10 stepper motor revolution [according to my blind] to open and close the blind slat, which is i dunno how to program it.
... so even the switch is still in high, the stepper only rotate 10 times and stop and wait till the other state. The stepper motor that I use is common 1.8 degree per step.
The operation repeated until someone invoke the manual switch.
Other switch which is SW5-SW6 is to use to control blind vertical position by using simple DC motor interface to L293D which is will be added later on. The LCD 16x2 is only to display operations, since PIC16F877A still have the unused port.
p/s: If someone interested in this project or feel free to help, just pm me to get the proteus VSM files. Since the dateline is only a week, I hope someone can help me urgently..Thanks in advance!
Bookmarks